Table of Contents
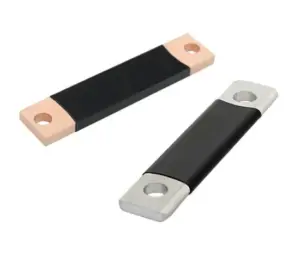
C-Fit Copper is one of the leading manufacturers and exporters of copper bus bars in Kuwait known for its high quality products. Established as a reliable company with a strong focus on quality and accuracy, we offer a wide variety of copper bus bars that meet the requirements of various industries including electrical, automotive, and construction. Our bus bars are characterized by enhanced conductivity, high durability, as well as the ability to resist corrosive action, making them suitable for application where conditions are tough.
At C-Fit Copper, we maintain superior quality and use hi-tech fabrication techniques to manufacture our copper bus bars to match international standard. C-Fit Copper aspires to achieve customer satisfaction with the help of our esteemed team of specialists to become one of the leading companies that supply the copper bus bar in Kuwait.
Types in Copper Bus bars:
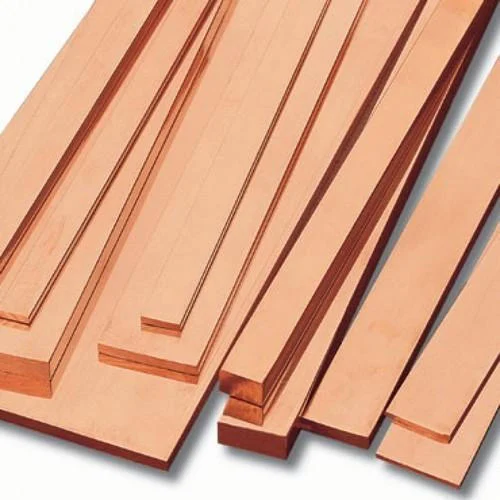
Flat Copper Bus bars in Kuwait
Flat bus bars are electrical conductors of rectangular section where the flatness of the Copper bus bars provides high conductivity and low electrical resistance, low thermal resistance and easy to incorporate into small electrical structures.
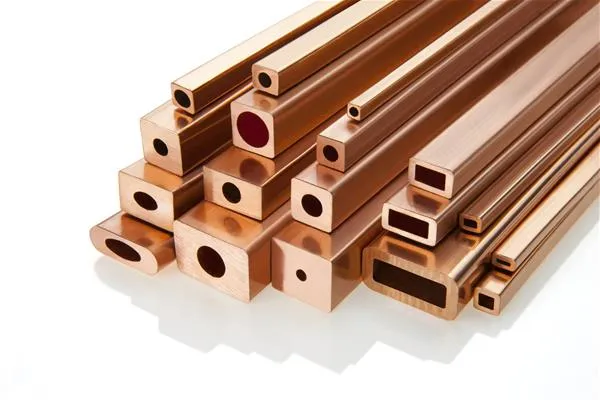
Hallow Copper Bus bars in Kuwait
Hollow conductors are light and versatile primarily employed in electrical networks. The effectively provides systems for cooling, low utilization of material and good conductivity makes them appropriate for high current usage.
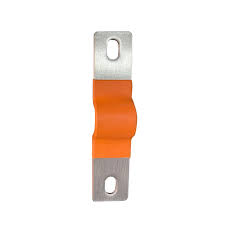
Insulated Copper Bus bars in Kuwait
Insulated bus bars are effective in the power distribution since they minimize chances of electric shock and short circuits. They offer simultaneously good conductivity and strong dielectric properties that make the risk and failures negligible.
Copper Bus Bars Specification
Copper bus bars usually use standardized dimensions keeping in mind optimal performance and fitting properly within the electrical system. The specifications which are provided include material composition, whether it is copper or aluminum as well as various grades of purity levels for conductivity. Besides, bus bars as well are specified by dimensions in which the thickness, width, and length are designed for current carrying capacity and space limitations of the application. Surface finish, for corrosion resistance and electrical contact are also required to be specified such as tin plating or bare copper.
Copper Bus Bars Specification | ||
---|---|---|
Dimension Details :- | Thickness 1 mm (min) 2 mm (min) 3 mm (min) 5 mm (min) 6 mm -50 mm | Width 10 mm – 50 mm 10 mm – 100 mm 10 mm – 150 mm 10 mm – 200 mm 10 mm – 250 mm |
Specifications (ETP) :- | IS: 191, 613 & 1897, BS EN 13601:2002, ASTM B187 | |
Cross section :- | upto 3000 mm² | |
Standard :- | EN 13601: 2002, EN 13602: 2002 | |
Conductivity :- | Above 97% IACS min in Half Hard Above 99.95% in annealed | |
Purity :- | Copper – 99.9% | |
Specifications (OFC) :- | Copper: 99.99%, O 2: < 10 ppm Copper: 99.90%, O 2: < 100 ppm | |
Type :- | Rectangular, square and any corner radius, Full Round Edge |
Features of Copper Bus Bars
- High Electrical Conductivity: Provisions for effective power distribution with reduced losses on the electrical power.
- Durability: Durable and having the ability to be long-lasting for long periods and can endure extreme environmental conditions.
- Corrosion Resistance: Optimizes performance over time, especially in corrosive environment.
- Thermal Conductivity: Designed to prevent overheating by efficiently releasing the heat generated inside the processor.
- High Current Capacity: High current handling capability making them ideal for applications that require high performance.
Material E-copper F30 current load in A | Material E-AL current load in A | |||||||||||
---|---|---|---|---|---|---|---|---|---|---|---|---|
width x thickness mm | weight kg/ meter | AC up to 60 Hz bar | DC + AC up to 16 2/3 Hz bar | weight kg/meter | AC up to 60 Hz bar | DC + AC up to 16 2/3 Hz bar | ||||||
uncoated | painted | uncoated | painted | uncoated | painted | uncoated | painted | |||||
40 | x | 3 | 1,070 | 366 | 435 | 367 | 436 | 320 | 285 | 346 | 285 | 346 |
25 | x | 5 | 1,115 | 327 | 384 | 327 | 384 | 340 | 255 | 305 | 255 | 305 |
30 | x | 5 | 1,340 | 379 | 447 | 380 | 448 | 410 | 295 | 356 | 296 | 356 |
20 | x | 10 | 1,780 | 427 | 497 | 428 | 499 | 540 | 331 | 393 | 331 | 393 |
40 | x | 5 | 1,780 | 482 | 573 | 484 | 576 | 540 | 376 | 456 | 376 | 457 |
50 | x | 5 | 2,230 | 583 | 697 | 588 | 703 | 680 | 455 | 556 | 456 | 558 |
30 | x | 10 | 2,670 | 573 | 676 | 579 | 683 | 810 | 445 | 536 | 447 | 538 |
60 | x | 5 | 2,670 | 688 | 826 | 696 | 836 | 810 | 533 | 655 | 536 | 658 |
40 | x | 10 | 3,560 | 715 | 850 | 728 | 865 | 1,080 | 557 | 677 | 561 | 682 |
80 | x | 5 | 3,560 | 885 | 1070 | 902 | 1090 | 1,080 | 688 | 851 | 694 | 858 |
50 | x | 10 | 4,450 | 852 | 1020 | 875 | 1050 | 1,350 | 667 | 815 | 674 | 824 |
100 | x | 5 | 4,450 | 1080 | 1300 | 1110 | 1340 | 1,350 | 846 | 1050 | 858 | 1060 |
60 | x | 10 | 5,340 | 985 | 1180 | 1020 | 1230 | 1,620 | 774 | 951 | 787 | 966 |
80 | x | 10 | 7,120 | 1240 | 1500 | 1310 | 1590 | 2,160 | 983 | 1220 | 1010 | 1250 |
100 | x | 10 | 8,900 | 1490 | 1810 | 1600 | 1940 | 2,700 | 1190 | 1480 | 1240 | 1540 |
120 | x | 10 | 10,680 | 1740 | 2110 | 1890 | 2300 | 3,240 | 1390 | 1730 | 1460 | 1830 |
160 | x | 10 | 14,240 | 2220 | 2700 | 2470 | 3010 | 4,320 | 1780 | 2220 | 1900 | 2380 |
200 | x | 10 | 17,800 | 2690 | 3290 | 3040 | 3720 | 5,400 | 2160 | 2710 | 2350 | 2960 |
12 | x | 2 | 210 | 108 | 123 | 108 | 123 | 60 | 84 | 97 | 84 | 97 |
15 | x | 2 | 270 | 128 | 148 | 128 | 148 | 80 | 100 | 118 | 100 | 118 |
20 | x | 2 | 360 | 162 | 189 | 162 | 189 | 110 | 127 | 150 | 127 | 150 |
15 | x | 3 | 400 | 162 | 187 | 162 | 187 | 120 | 126 | 148 | 126 | 148 |
20 | x | 3 | 530 | 204 | 237 | 204 | 237 | 160 | 159 | 188 | 159 | 188 |
25 | x | 3 | 670 | 245 | 287 | 245 | 287 | 200 | 190 | 228 | 191 | 228 |
30 | x | 3 | 800 | 285 | 337 | 286 | 337 | 240 | 222 | 267 | 222 | 268 |
20 | x | 5 | 890 | 274 | 319 | 274 | 320 | 270 | 214 | 254 | 214 | 254 |
Dimension Chart:
Width * Height (W*H) | (W*H) sqmm | (W*H) sqmm |
---|---|---|
25*05 | 60*05 | 100*08 |
30*05 | 60*08 | 100*10 |
30*08 | 60*10 | 100*12 |
35*05 | 70*05 | 110*08 |
35*08 | 70*08 | 110*10 |
40*05 | 70*10 | 110*12 |
40*08 | 70*12 | 120*08 |
40*10 | 80*05 | 120*10 |
50*05 | 80*08 | 120*12 |
50*08 | 80*10 | |
50*10 | 80*12 |
Advantages And Disadvantages
Advantages
- High Conductivity: This distribution of electrical power happens efficiently with the least amount of energy lost in the process.
- Compact Design: Conserves space through centralization with cables and minimizes compartmentalization of cables.
- Durability: Durable and effective for long term use that can able to be used under severe conditions.
- Ease of Installation: Reduces the degree of difficulty in the wiring process of electrical systems and their alterations.
- High Current Capacity: Capable of handling high current levels, ideal for use in demanding circuits.
Disadvantages
- Cost: However, they are relatively costly as compared to the conventional wiring techniques.
- Weight: It is generally heavier, which means it needs support to be stronger than the traditional N gauge.
- Potential for Overheating: Has the potential of overheating if not well continuously managed or if it poorly designed.
- Complexity: Tomer specific designs may be challenging and may even call for sophisticated engineering techniques.
- Limited Flexibility: They can only be stretched to a limited extend and hence a bit bulky to bend in tight corners as compared to cables.